I started off by measuring the model with a digital caliper. I'm only doing one piece as I go. Starting with the shield as it looked like the easiest and a good evaluating piece for scale. I'm drawing everything up in 3d in AutoCad. Then I break up the model in flat panels and dimension them. Its a bit tedious but I don't mind. (I'm an engineer after all.)
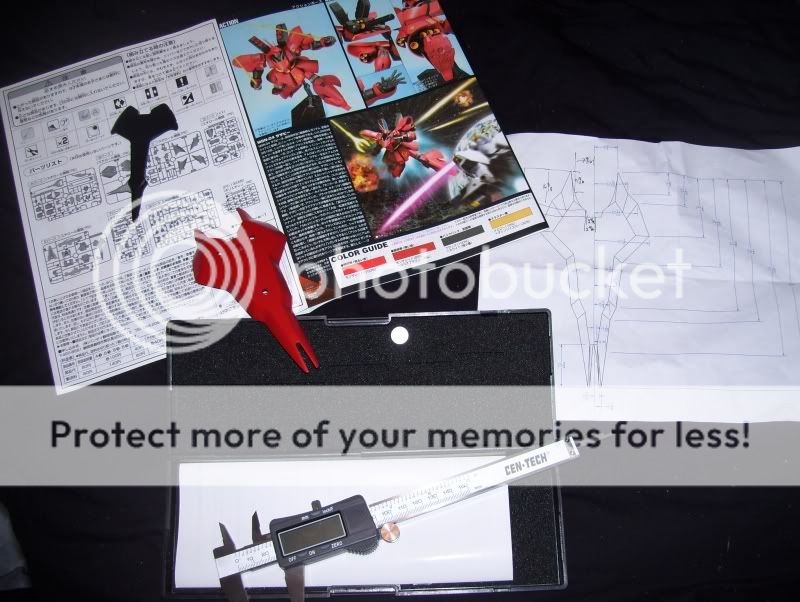
For the actual construction I am using DOW's polystyrene foam that you pick up from a home improvement store like Lowes or Home Depot. It usually comes in the colors pink or blue. (Mines blue) To adjoin the pieces together I'm using 3M spray glue. Make sure its the one that has acetone as the major ingredient. The other products will dissolve the foam. For edge seam construction I'm just using a low temp glue gun. Now the foam is pretty stiff but if press hard still can mar pretty easy. So I had to cover it with something really stiff and thin (and cheap). US plastics has a great product called "High Impact Styrene Sheet" It's actually just really thin ABS plastic. It comes in many thicknesses so I chose the .030". That's a little less than 1/32". This will stiffen the foam board and make it much more dent resistant. It also allows me to use spray paint for the coloring as directly spraying on the foam would melt it.
This is a big project, and so it takes up a lot of room. Room I don't have in my tiny place. So the construction site is my driveway out in the elements.

I have a large folding table I set the foam on and as you can see have begun marking out the profile of the base of the shield with a Sharpie. The Minwax cans are just weights. I basically drew the center line and marked all the corners (Be sure to keep squared!) and then played connect the dots.
I'm sure there are tons of ways to cut this stuff, but I think a fine toothed saw is best. (Don't use a carpenters knife its too thick) I used a steel hacksaw. It worked wondrously.

Now there are a lot of smooth corners in this model and I can get close by sanding or filing the foam down, but to get a really nice surface I needed something. So I decided to get a quart of Bondo. I thought about using DryWall spackle but figured it would have a tendency to crack with me moving in the suit. I've never worked with Bondo before but knew the concepts from some gearhead buddies of mine. I just tested a fillet weld or corner joint to get the "feel" of how the stuff would work. Its pretty soupy for a few minutes then gets pretty tacky and stiff. It sure does smell good too. Ahhhhhh. No seriously do this in a well ventilated area or wear a respirator or both. The fumes are toxic and toxic stuff is bad. It was rock hard within an hour and then your suppose to sand it down smooth. But since it was getting late and work starts early in the morning I decided to leave it for another day.
No comments:
Post a Comment